Improving the Energy Efficiency of ESPs Using Sine-Wave Rather Than Six-Step Drives
by Jim Lousier hardware development manager
While six-step drives continue to be specified in electric submersible pumping (ESP) systems, their selection inadvertently penalizes their users through increased energy costs. Sine-wave drives offer an improvement in efficiency of 2% or more over traditional six-step control.
The overall energy efficiency of an ESP system is a function its components, which include the variable-frequency drive, step-up transformer, motor cable, submersible motor, and pump. Since this value can often be as low as 50%, there is great incentive to improve the performance of these individual components. One aspect that should not be overlooked in the quest for greater efficiency is the method of excitation used to power the ESP.
Historically, six-step waveforms were originally used with AC drives due to the poor switching characteristics of early semiconductor power devices. The low switching frequencies of these six-step drives (360 to 540 Hz at typical excitation frequencies of 60 to 90 Hz) was an advantage with ESP applications because it produced tolerable motor voltage spikes with long motor cables. In contrast, today's variable-frequency drives use a technique called pulse-width modulation (PWM) to switch modern semiconductors at very high speeds (2,000 to 8,000 Hz) to produce smooth, sinusoidal waveforms ideal for operating transformers and motors.
While PWM drives have replaced six-step drives in nearly all surface-driven artificial lift systems, confusion remains as to which approach is most energy efficient with ESP systems. That confusion generally centers around the output filters used on PWM drives to remove the switching-frequency ripple from the sine-wave outputs. Those filters completely remove switching transients that can stress cable and motor insulation. In fact, they reduce voltage stress about 40% from that found in six-step drives. While output filters introduce power losses that might be expected to lower overall energy efficiency, the use of sine-wave rather than six-step voltages reduces losses in other parts of the system that more than offset the filter loss.
Six-step drives produce distorted motor currents that can have harmonic currents as large as 40% of the useful motor fundamental current. This total harmonic distortion (THD) produces additional heat losses in the transformer, cable, and motor that reduce overall system efficiency. Sine-wave drives, on the other hand, have virtually no harmonic distortion but do suffer some additional losses from their output filters. The important issue is the reduction of six-step harmonic losses relative to the added sine-wave filter losses.
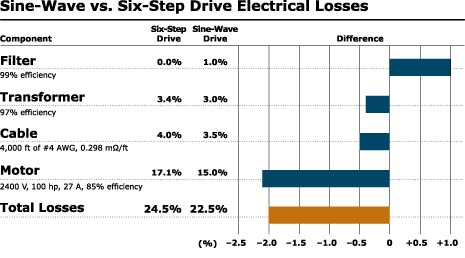
The example above illustrates the potential improvement in overall energy efficiency using sine-wave rather than six-step drives on a typical ESP system. Pump hydraulic and mechanical efficiencies were left out of the example to focus on electrical efficiency. Sine-wave drives also provide other improvements in the efficiency of the electrical supply that have been ignored for simplicity.
From the results, it can be seen that sine-wave drives improve the overall energy efficiency of ESP systems by 2% relative to their six-step predecessors. Six-step drives produce significant current distortion that increases transformer, cable, and motor losses. By reducing output current harmonic distortion, sine-wave drives increase overall system efficiency despite added losses from using an output filter. Sine-wave drives also shift losses away from downhole components to surface output filters, which lowers heating and increases the reliability of downhole components.
The improved power factor of sine-wave drives can also decrease utility installation and operating costs. Sine-wave drives provide a near-unity power factor at all combinations of line voltage, pump load, and motor speed. In contrast, six-step drive power factors can fall far short of unity for a variety of conditions. Reduced power factors increase losses in the electrical supply may reduce overall energy efficiency by several additional percent and can also lead to utility-imposed power-factor penalties.
For an example of the kinds of stiff penalties imposed by power companies for power quality issues, see the related article on meeting utility harmonic regulations in Issue 3 of Solutions.
For more information on saving energy with sine-wave drives, please contact us.
Go to top
Capture and Display Rod-Pump Dynamometer Graphs Using a Palm Pilot
One of the outstanding features of Unico's sucker-rod pump drives is their ability to generate both surface and pump dynamometer graphs. With Unico's new Drive Chart program, well operators can easily capture dynamometer graphs in the field using a Palm Pilot or other handheld, then take them back to the office for backup, analysis, and printing.
|